Heat exchangers are vital components in various industrial processes, ensuring efficient heat transfer between fluids. However, cracking in heat exchangers can lead to severe operational problems, downtime, and potential hazards. Understanding the causes of cracks and effectively repairing them is crucial for maintaining optimal performance and preventing further damage. This comprehensive guide will provide a step-by-step approach to identifying, repairing, and preventing cracked heat exchanger issues.
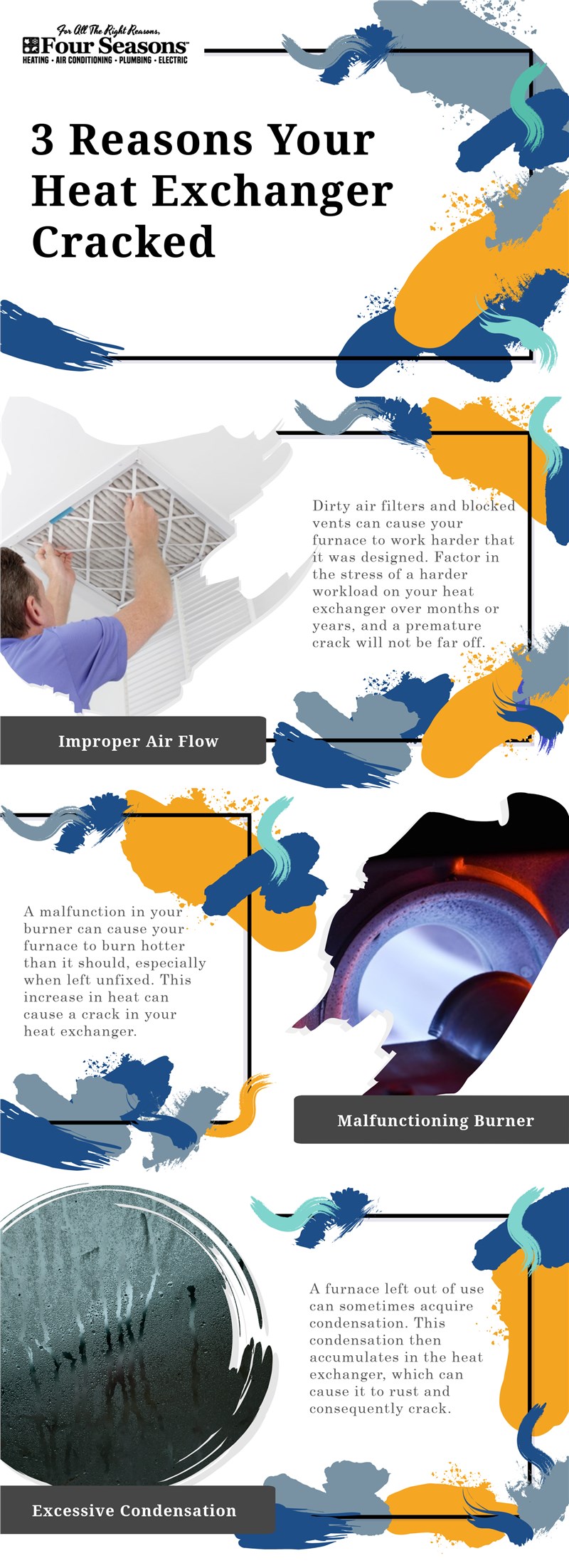
Image: www.fourseasonsheatingcooling.com
Identifying a Cracked Heat Exchanger: Signs and Causes
Cracks in heat exchangers can manifest in various forms, from microscopic fissures to large, visible ruptures. Common signs of a cracked heat exchanger include:
- Pressure drop between the inlet and outlet fluids
- Fluid leakage or dripping
- Reduced heat transfer efficiency
- Unusual noises or vibrations
- Corrosion or deposits on the heat exchanger surface
Cracks can arise due to several factors, including:
- Mechanical stress from thermal expansion and contraction
- Pressure fluctuations or sudden pressure spikes
- Corrosion and erosion from harsh process fluids
- Manufacturing defects or material flaws
- Inadequate maintenance or improper operation
Step-by-Step Repair Process for Cracked Heat Exchangers
1. Safety Precautions
Before attempting any repair, ensure your safety by following proper protocols:
- Shut down the system and isolate the heat exchanger.
- Depressurize the system and drain all fluids.
- Wear appropriate personal protective equipment (PPE), including gloves, eye protection, and a respirator.
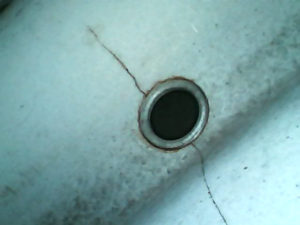
Image: www.tmscomfort.com
2. Crack Location and Inspection
Identify the exact location of the crack using a visual inspection or non-destructive testing (NDT) methods like liquid penetrant testing or ultrasonic testing. Thoroughly examine the surrounding areas for additional cracks.
3. Crack Preparation
Prepare the cracked area for repair by removing any corrosion, scale, or debris. Use a wire brush or sandpaper to clean the surface and obtain a smooth, clean base for welding or patching.
4. Welding Repair
For small cracks, welding is a common repair technique. TIG (Tungsten Inert Gas) welding is typically used for its precision and ability to create strong, sealed welds. Ensure proper joint preparation, cleaning, and welding technique to prevent further cracking.
5. Patching Repair
Patching is suitable for larger cracks or areas with extensive damage. Weldable metal patches or epoxy resins can be used to cover the crack and restore the heat exchanger’s integrity. Follow the manufacturer’s instructions carefully for effective patching.
6. Pressure Testing and Reassembly
Once the repair is complete, conduct a pressure test to verify the effectiveness of the repair and ensure no further leaks. Reassemble the heat exchanger and restore it to operation, following proper installation procedures.
Preventing Heat Exchanger Cracks: Best Practices
To minimize the risk of heat exchanger cracks, implement the following best practices:
- Proper Design and Selection: Ensure heat exchangers are designed and selected for the specific application, considering factors like pressure, temperature, and fluid compatibility.
- Regular Inspection and Maintenance: Schedule periodic inspections and maintenance to identify and address potential issues early on, preventing small cracks from escalating into major failures.
- Corrosion Control: Implement corrosion control measures such as water treatment, chemical inhibition, and cathodic protection to mitigate the effects of corrosive fluids on the heat exchanger’s surface.
- Monitoring and Control: Establish a monitoring system to track operating parameters like pressure, temperature, and flow rates. Implement control mechanisms to prevent pressure surges and temperature fluctuations that could induce stress on the heat exchanger.
- Training and Operator Education: Train operators on proper operating procedures, including startup, shutdown, and emergency response protocols to minimize the risk of human error and mishandling.
How To Fix A Cracked Heat Exchanger
Conclusion
Cracked heat exchangers can lead to downtime, reduced efficiency, and potential hazards. By understanding the causes and signs of cracking, following proper repair techniques, and implementing preventive measures, businesses can minimize the occurrence of such issues and maintain the optimal performance of their heat